Visiting the Importance of Visibility & Collaboration in Supply Chains
https://morailogistics.com/visiting-the-importance-of-visibility-collaboration-in-supply-chains/
Two new studies were published earlier this month that looked at supply chain visibility and collaboration.
Supply Chain Visibility & Collaboration Study
The first study by ARC Advisory group titled Supply Chain Visibility & Collaboration Study surveyed 200 organizations from a wide range of industries.
The researchers defined supply chain collaboration as “having a collaborative, multi-supplier, multi-tier, supply chain planning solution” writes Steve Banker in this Forbes article covering the study. “For visibility, the definition was a solution providing visibility to the order process (order placed, order adjusted, order accepted), inventory at rest or inventory in motion events, or supply chain risks, or providing a stand-alone supply chain analytics/event management solution not embedded in other solutions” he continues.
The survey asked respondents to weigh in on issues such as inventory visibility, supply chain costs, new enterprise resource planning integration, responsiveness to customer demands with specific focus on strategic questions such as,
- Why have B2B network suppliers emerged as leaders in this market?
- How will Internet of Things data be leveraged by these solutions?
- How will these solutions affect the next generation of supply chain software platforms?
- What are the niche solutions poised to grow rapidly in this market place?
What the survey finds is that not only visibility and collaboration software is growing very rapidly, but that B2B network solutions specifically (for both visibility and collaboration) is what’s driving the market’s rapid growth.
The ROI with visibility projects has to do with SCP applications improving service levels with less inventory.
“The more companies can reduce their lead times, and the less variability there is surrounding those lead times, the better the ROI that can be achieved with SCP tools. Supply Chain Visibility, provides the data and metrics surrounding lead-times, and then allows Lean practitioners to work with supply chain partners to improve and control those lead-times” writes Banker. Another reason why visibility is so important is supply chain orchestration. Through orchestration, a company is able to balance supply-demand in reaction to surges as well as deal with supply disruptions more promptly.
University of Tennesee Global Supply Institute Study
The second study published by the University of Tennessee’s Global Supply Institute, in collaboration with B2B integration provider DiCentral. The study involved surveying over 200 organizations of various sizes and asking respondents to weigh in on issues such as inventory visibility, supply chain costs, new enterprise resource planning integration, and responsiveness to customer demands.
The study found that to increase business flow efficiency and cut cost, many companies are investing in B2Bi (business to business electronic integration).
“Of those surveyed, 94 percent saw significant improvement in their electronic connectivity capabilities and 68 percent reported that their clients said they were easier to do business with after using cloud-based B2Bi managed services” write the researchers.
The findings of the study echo those of the ARC group in so far that lead times are reduced, forecast accuracy improves, and supply chain reactivity improves when visibility & collaboration becomes a focus. For example, from one of the case studies the study cites,
An office supplies retailer surveyed for the study invested time and technology to collaborate more effectively with a major supplier, and as a result, in-stock fill rates rose significantly—to nearly 99 percent from below 95 percent. Lead times reduced nearly 60 percent. Forecast accuracy improved by more than 30 percent, and inventory turnover increased 9 percent
That’s it for us this week! If you liked this blog post, why not subscribe to our blog? If you’re interested in what we do as a 3rd party logistics provider, don’t hesitate to check out our services (as expressed above, we are very pro finding you the lowest total cost!). We’re also in the twittersphere, so give us a follow to get the latest logistics and supply chain news.
12 Key Facts About the Driver Shortage and the Future of the Trucking Industry
https://morailogistics.com/12-key-facts-about-the-driver-shortage-and-the-future-of-the-trucking-industry/
The current shortage of truck drivers is estimated at roughly 25,000. The turnover rate, which hit 96% by the end of 2014 is due to a multitude of reasons, including demographic, regulatory, and the fact that drivers are away from home for a period of time, among other factors.
This month, we thought it would be a great idea to take a look at these facts and figures!
12 Key Facts About the Driver Shortage and the Future of the Trucking Industry

That’s it for us this week! If you liked this blog post, why not subscribe to our blog? If you’re interested in what we do as a 3rd party logistics provider, don’t hesitate to check out our services (as expressed above, we are very pro finding you the lowest total cost!). We’re also in the twittersphere, so give us a follow to get the latest logistics and supply chain news.
Getting the Chocolate to Melt in your Mouth, Not on a Pallet
https://morailogistics.com/getting-the-chocolate-to-melt-in-your-mouth-not-on-a-pallet/
Almost anything can be purchased online. Items such as books, movies, clothing, cameras and groceries are just a few clicks away from consumers. With services such as one hour delivery or similar offered by Amazon and other companies, customers can be sure that they won’t have to wait long before receiving their items. Best part of all, because the items usually come straight from the manufacturer, the prices are usually competitive.
But did you know that chocolate, a relatively common treat enjoyed by so many, presents a big logistics problem for companies that are trying to offer individual deliveries?
The issue has to do with heat. During the summer months and in warmer climes, chocolate will melt or “bloom” which is when fat in the chocolate rises to the top and leaves a white discoloration. It is for this reason that refrigeration is so important when shipping large shipments of chocolate across long distances. However, the economy of scale that offsets the costs of refrigeration goes away as shipments become smaller. So although the holidays are a popular time to give chocolates as gifts, chocolate makers are not typically making the profits that those outside their business would expect from the surge of orders seen around Valentine’s Day, Christmas and Easter.
Customers expect to be to purchase items online and chocolate companies want to meet those expectations. It comes at a cost though as Robbie Whelan explains in this writes in Wall Street Journal:
Keeping a small shipment of chocolate cool can cost more than the product itself. Hershey charges $6.95 to ship a $4.25 bag of Kisses ordered on its website. In a notice on the site, the Pennsylvania-based maker of Kit Kat and Reese’s also “strongly suggests” that customers buy liquid ice packs and a foam cooler for an additional $4.99. That, plus the recommended expedited shipping, would bring the cost to $20.20, before taxes.
As sales for chocolate grows, the volume of individual orders and sales will continue going up. For example, between 2010 to 2015 overall online chocolate sales grew over 80% in the U.S. Chocolate is also seeing a rise in sales internationally as countries such as China are consuming chocolate and growing rates.
Europe is also seeing a surge in chocolate sales with the UK as its export of chocolate to Switzerland has increased 160% in just the last four years. The UK has become a major exporter of chocolate both within Europe and for emerging economies.
“Overall, U.S. online chocolate sales rose more than 80% between 2010 and 2015, to $341.7 million annually, according to data provider Euromonitor International, and e-commerce represented 1.9% of all chocolate sales last year, up from 1.2% five years earlier” writes Whelan.
There are attempts at bringing down the costs of online shipments. Last month, Hershey accepted its final entries in a competition with a prize of $25,000 for whoever designs the lightest, most-affordable packaging to keep chocolate from melting for at least 48 hours. It hasn’t announced the results.
That’s it for us this week! If you liked this blog post, why not subscribe to our blog? If you’re interested in what we do as a 3rd party logistics provider, don’t hesitate to check out our services (as expressed above, we are very pro finding you the lowest total cost!). We’re also in the twittersphere, so give us a follow to get the latest logistics and supply chain news.
EYEFREIGHT GUEST POST: Shortage of Top-Level Logistics Talent Underscores the Need to Shatter ‘Glass Ceiling’
https://morailogistics.com/eyefreight-guest-post-shortage-of-top-level-logistics-talent-underscores-the-need-to-shatter-glass-ceiling/
By Lisa Henthorn
Virtually impenetrable not all that long ago, the “glass ceiling” blocking women from executive-level jobs in the logistics and supply chain industry appears to be shattering.
Though few (if any) people in our industry would argue that our historic gender bias has gone away, the outlook for women is considerably brighter these days than it was when Industry Week made this bleak observation a little over two years ago:
Half of the human population is female. More than half of all university students in the United States are female. Around a third of all MBA students, including those concentrating on supply chain studies, are female. And yet, when (we) did a manual count of top supply chain executives in Fortune 500 companies, we found only 22 women among 320 businesses that had a true supply chain function.
22 out of 320? That’s a definitive “F-minus,” but there’s growing evidence that our industry’s grade on gender equality is improving. Among the most significant signs: U.S. Secretary of Transportation Anthony Foxx appointed Michelle Livingstone to a two-year term on the National Freight Advisory Committee.
Livingstone, by the way, is VP of Transportation for Home Depot. As such, she’s on a growing roster of females who hold top-level logistics posts at high-profile companies. The list also includes:
- Ann Ackerson, VP of Worldwide Supply Chain for Dresser-Rand, which recently merged with Siemens
- Shari Boston, VP, Global Supply Chain, at ConvaTec
- Lillian Dukes, VP of Business Operations for Global Customer Support and Services at Spirit AeroSystems
- Sandra Evett, VP, Customer Service & Logistics, at Kraft Foods
- Beth Ford, EVP and Chief Supply Chain and Operations Officer for Land O’ Lakes
- Laurel Junk, VP of Supply Chain Management at Kaiser Permanente
- Debbie Lentz, Chief Supply Chain Officer for Toys “R” Us
- Mary Long, VP of Logistics and Network Planning for Domino’s Pizza
- Susan Pechellio, recently named VP of Global Transportation for Starbucks — and prior to that, VP of Transportation and Supplier Collaboration at Staples
- Kathryn Wengel, Worldwide President of Johnson & Johnson Supply Chain
- Trish Young, VP of North America Supply Chain for Nike.
These executives deserve our applause. And the companies that gave them their respective titles should get a pat on the back, too. Why? If for no other reason, it’s because they decided to break with the “old-boy network” tradition that lingers on in our industry and give leadership roles to the people most qualified to have them. This simply makes good business sense, and in light of our industry’s ominous talent shortage, that’s especially true.
In other words, as we look for answers to the labor shortage, there’s no time like the present to tap the female labor pool.
Lisa Henthorn is a vice president at Eyefreight, a provider of transportation management system technology. Lisa can be reached at l.henthorn@eyefreight.com
About Eye Freight
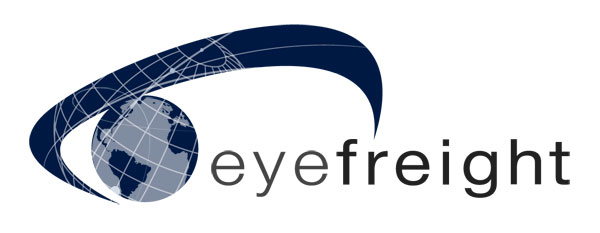
The Eyefreight SaaS TMS is a Level 5 TMS, providing shippers with a control tower for central coordination and detailed visibility over multi-modal, multi-leg, international logistics. Eyefreight runs proprietary algorithms to manage and monitor the entire logistics process – optimizing inventory allocation and distribution planning, and unlocking traditional bottlenecks within the logistics function.
A Look At Some Fun Logistics Facts & Figures For St. Patrick’s Day
https://morailogistics.com/a-look-at-some-fun-logistics-facts-figures-for-st-patricks-day/
For this St. Patrick’s Day, we would like to list some interesting facts and figures regarding this popular holiday. It isn’t only green hats and green beer that makes this national holiday celebrated in more countries than any other national festival, but also some behind the scenes logistical planning!
About the holiday
Although green is associated with the holiday today, it wasn’t always the case. For many years, blue was the color most often associated with St. Patrick as green was considered unlucky. St. Patrick’s blue was considered symbolic of Ireland for many centuries and the Irish Presidential Standard is still blue. Green became associated with Saint Patrick’s Day because it is the color of spring, of Ireland, and of the shamrock.
Did you know that this holiday known for green beer and the 13 million pints of Guinness to be consumed this year, used to be a dry holiday? Mental Floss gives a bit of history in this article,
For most of the 20th century, Saint Patrick’s Day was considered a strictly religious holiday in Ireland, which meant that the nation’s pubs were closed for business on March 17. (The one exception went to beer vendors at the big national dog show, which was always held on Saint Patrick’s Day.) In 1970, the day was converted to a national holiday, and the stout resumed flowing.
As already mentioned, despite it being a national holiday, St. Patrick’s Day is celebrated in many countries. Among them is the United States which held the very first St. Patrick’s Day parade was not in Ireland. It was in Boston in 1737. Chicago is noteable as it goes so far as to dye its river green for several hours in celebration.
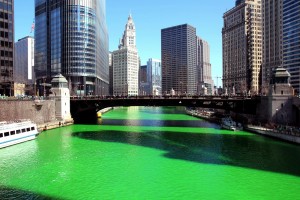
St. Patrick’s Day consumer trends
The National Retail Federation (NRF) had Prosper Insight and Analytics conduct the NRF 2015 St. Patrick’s Day Spending Survey. The survey was designed to gauge consumer behavior and shopping trends related to St. Patrick’s Day.
Here are the highlights:
- Nearly 127 million Americans are planning to celebrate the traditional Irish holiday and will spend an average of $36.52 on green garb, festive food and more, compared to $35.78 last year.
- Total spending for the holiday, which fell on Tuesday, March 17, is expected to reach around $4.6 billion.
- The survey found that more than 104 million Americans, or eight in 10 (82.4%) of those celebrating, plan to wear green to make sure the luck of the Irish is with them this year; 28.9 million, or 22.8% of celebrants, plan to decorate their homes with shamrocks, leprechauns and pots of “gold.”
- 29.2 percent – 37 million Americans – plan to celebrate at a bar or restaurant and 19 percent (24 million consumers) plan to attend a private party; an additional 30 percent plan to make a special dinner to commemorate the Irish holiday.
And here’s a bonus fun fact: The estimated statistical odds of finding a four-leaf clover on your first try is 10,000 to 1!
Erin go Bragh!
That’s it for us this week! If you liked this blog post, why not subscribe to our blog? If you’re interested in what we do as a 3rd party logistics provider, don’t hesitate to check out our services (as expressed above, we are very pro finding you the lowest total cost!). We’re also in the twittersphere, so give us a follow to get the latest logistics and supply chain news!
3 Reasons Why a Social Media Strategy Will Help Your Brand in Logistics and Supply Chain
https://morailogistics.com/3-reasons-why-a-social-media-strategy-will-help-your-brand-in-logistics-and-supply-chain/
Many businesses have embraced social media to grow and to bring value to both their company and their customers. This is because the number of people online has been rapidly growing since the 2000s. Within the United States for example, 70% of the population have at least one social networking profile.
For companies involved in 3PL and logistics, this means a well-crafted social media strategy can afford them new avenues improve their brand visibility, engage their customers, and to increase their involvement in how the industry itself is perceived. All of these lead to a stronger brand name.
This month’s ebook focuses on how social media helps your brand in the logistics and supply chain industry!
3 Reasons Why a Social Media Strategy Will Help Your Brand in Logistics and Supply Chain
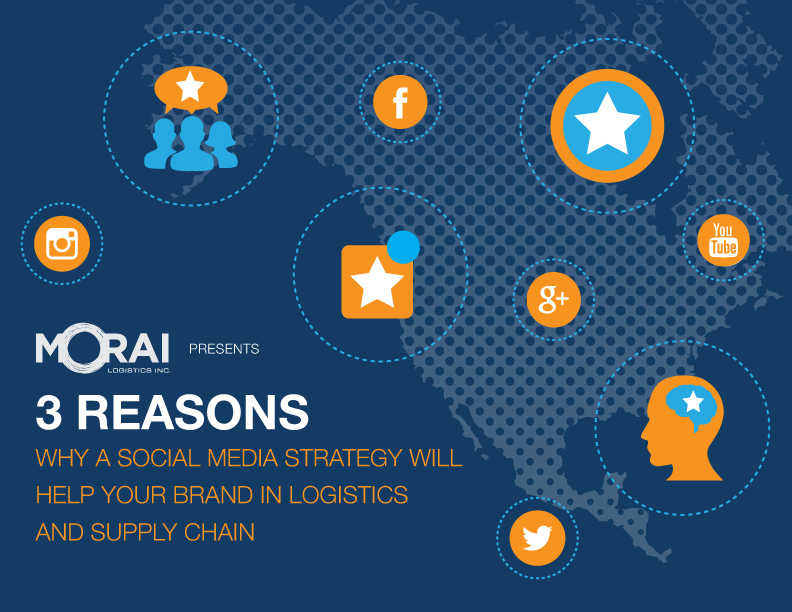
That’s it for us this week! If you liked this blog post, why not subscribe to our blog? If you’re interested in what we do as a 3rd party logistics provider, don’t hesitate to check out our services (as expressed above, we are very pro finding you the lowest total cost!). We’re also in the twittersphere, so give us a follow to get the latest logistics and supply chain news!
WE’RE HIRING: Client Success Specialist – 3PL
https://morailogistics.com/were-hiring-client-success-specialist-3pl/
Morai Logistics is currently looking for a full-time Client Success Specialist to join our team in Mississauga, ON.
View the job posting on Indeed by clicking here!
What does that even mean?
Logistics can be messy, as a client success specialist, your goal is to deliver success within the chaos. On a day-to-day basis, you will be primarily responsible for coordination of the movement of goods from point A to point B (origin to destination). That means, though isn’t necessarily limited to, reserving and booking container equipment from various transportation providers (rail, truck, etc.), coordinating with drayage carriers (and knowing what drayage means!), and electronic tracking (we work with Triton) and tracing, billing, etc.
Our Core Values
- Integrity and Honesty
- Respect
- Empowerment
- Client Success
- Community
The top candidates for this position are born multi-taskers and are experts at analyzing many different situations. They are customer/client-oriented. They’re also a great team player and know the difference between casual and professional writing and when to use each!
What Your Main Responsibilities Would Be
- Acting customer support and administrative representative for a set of clients
- Monitors clients’ equipment usage, costs, containers, etc.
- Prepares and analyzes reports on factors affecting the supply chain process (outstanding equipment charges, yard checks, etc.)
- Investigate and solve issues regarding any transportation delays
- Provides basic consultation to help clients find cost saving initiatives
Prerequisites for this Position
- Post-secondary education preferred
- Minimum 3 years’ experience in the logistics industry
- Experience in truckload, LTL, and intermodal
- Strong analytical and priority management skills
- Ability to work under pressure and in a constantly evolving and changing environment
- Ability to multitask
- Team player and a good communicator
Additional Desired Traits
- Excel and Word experts
- Computer literacy in general
- Interpersonal, conflict resolution and negotiating skills
- Problem solving and decision making skills
- Organizational, planning, multi-tasking skills
- Time management skills; ability to assign tasks, set priorities and resolve related conflicts
- Forecasting, scheduling and tracking skills
If this all sounds appealing to you, then don’t hesitate to shoot us an e-mail contact@morailogistics.stage-cc.com with the job position (Client Success Specialist – 3PL Position) as part of the subject line!
Logistics trades professionals (i.e. truck drivers, machine operators, etc.): This probably isn’t the job for you, but maybe you know someone who would be the perfect fit! Send them this link and we’ll take it from there! Thanks!
That’s it for us this week! If you liked this blog post, why not subscribe to our blog? If you’re interested in what we do as a 3rd party logistics provider, don’t hesitate to check out our services (as expressed above, we are very pro finding you the lowest total cost!). We’re also in the twittersphere, so give us a follow to get the latest logistics and supply chain news!
The West Coast Port Labour Dispute: One Year Later
https://morailogistics.com/the-west-coast-port-labour-dispute-one-year-later/
It was around this time last year when the West Coast Port labour dispute was in full swing and many different businesses both in North America and abroad were feeling the effects. What had started as tensions between the International Longshore and Warehouse Union and the Pacific Maritime Association, led to negotiations failing over wage and labour conditions. From October 2014 to March 2015, the port’s ability to effectively and efficiently process cargo was severely impacted as several cargo-laden ships were not unloaded and instead left stranded up and down the coast.
Several companies were unable to ship their products in a timely manner leading to the accumulation of more and more extra supplies and products. This inventory glut crowded warehouses, eventually forcing companies to cut back on their new orders to clear out their backed-up storage facilities, costing several different businesses in the short and long-term. A new study by the Washington Council on International Trade came out this week and it analyzes the costs and impact of the labour dispute across multiple industries and sectors, including agriculture and food processing, retail, and transportation and manufacturing.
Several different estimates were forecasted at the time as to the cost of the slowdown. “Kurt Salmon consulting firm previously estimated the slowdown would cost U.S. retailers $7 billion. The Manhattan Institute conservative think tank projected apple farmers alone lost $19 million during each week of the slowdown. The North American Meat Institute estimated their losses to be more than $40 million each week” cites this article on USNews.com reflecting on the topic.
The study gives a breakdown as to the actual price tag for the slowdown which ended up being very significant for both the U.S economy, trade, and several different industries:
- U.S. exports dropped by more than $11 billion (nearly 6 percent) between May 2014 and February 2015.
- An estimated $558.8 million in exports were not shipped by water during those months. Some exporters diverted to air cargo, increasing shipments by air a total of $152.6 million.
- The value of goods that were not shipped during the period was $403.2 million.
- Importers racked up an additional $345.1 million in additional costs through reductions in inventory incurred by retailers, delayed delivery of components to manufacturers and so forth.
- Demurrage (storage) fees that would not have occurred if there were no port congestion totaled $7 million, and truck-idling costs of $14.2 million resulted.
- Fruit and meat rotted aboard idle West Coast ships, many of which were anchored off relatively warm ports like Los Angeles.
- Shipping companies rolled out surcharges upward of $1,000 per container on some ships to help cover expenses related to failed deliveries.
The total cost the study determined, is $769.5 million, however the council is very clear that this is only the short term cost. Long-term costs will be more far reaching. “Future costs, such as damaged client relations resulting in the loss of business or sole source contracts, can have long-lasting impacts on Washington businesses,” said the study. “While these impacts are not quantified in this report, they are real and potentially much greater than the near-term costs presented above.”
That’s it for us this week! If you liked this blog post, why not subscribe to our blog? If you’re interested in what we do as a 3rd party logistics provider, don’t hesitate to check out our services (as expressed above, we are very pro finding you the lowest total cost!). We’re also in the twittersphere, so give us a follow to get the latest logistics and supply chain news!
Recycling and Logistics
https://morailogistics.com/recycling-and-logistics/
The slippery slope of falling oil prices
In less than two years, the price of oil has gone from over $100, to just beneath $30 a barrel. The rapid price decline is having a major impact across most North American industries in one way or another. Most often, the exact net impact is complicated to determine because the industry or business may lose out in some areas, but benefit in others. However, when it comes to the business of recycling, the downward slide of oil prices has been unambiguous. The impact has been almost entirely negative. As oil prices continue to fall, so does the profitability of most companies who offer recycling services to cities and other businesses.
Though recycling is generally agreed by most consumers to be good for the environment, the actual cost of the process is something that isn’t discussed. Some of the costs involve emissions from shipping to be processed materials to recycling centers, which use a lot of energy and water. This means that the falling price tag of oil makes it so after a certain price point, it is simply cheaper for businesses to invest in creating new plastics and materials rather than recycle old ones.
“Abundant oil is the latest headache for recyclers. New plastics are made from the by-products of oil and gas production. So as plentiful fossil fuels saturate global markets, it has become cheaper for the makers of water bottles, yogurt containers and takeout boxes to simply buy new plastics”, writes the New York Times in this article. ” This, in turn, is dragging down the price of recycled materials, straining every part of the recycling industry” it continues.
New technology and new problems for sustainability efforts
The reduced price in oil isn’t alone in negatively impacting the recycling sector. As electronic products become ever smaller and cheaper, they are also impacting recycling cost and efforts:
Electronics devices contain less and less valuable materials and precious metals, which make reduce the size of economic urban mining opportunities. In itself, this isn’t a bad trend, but it does carry negative impacts when combined with designs that make materials harder to extract
The growing popularity of online shopping is also making itself felt in terms of environmental cost. In particular, the incredible amount of cardboard needed every day to meet consumer demand, and the subsequent freight that is needed to ship and deliver it. For some context, The United States alone produced 35.4 million tons of containerboard in 2014.
It’s not all bad
Despite the increasing cost tied to recycling plastics and other oil-based items rather than making new ones, some companies are still committing to their recycling and sustainability efforts. Some big companies such as Pepsi and Procter & Gamble are buying more recyclable material to meet sustainability goals. The online and e-commerce sector is also making strides towards lessening its environmental footprint according to Dennis Colley, the president of the Fibre Box Association — the trade group for the corrugated paper, or cardboard, industry — who states that 90 percent of corrugated packaging were recycled.
That’s it for us this week! If you liked this blog post, why not subscribe to our blog? If you’re interested in what we do as a 3rd party logistics provider, don’t hesitate to check out our services (as expressed above, we are very pro finding you the lowest total cost!). We’re also in the twittersphere, so give us a follow to get the latest logistics and supply chain news!
5 Questions to Ask Before Selecting a 3PL
https://morailogistics.com/5-questions-to-ask-before-selecting-a-3pl/
Third party logistics (3PL) companies offer resources for companies to outsource all or part of their supply chain management. When you select your 3PL you are essentially selecting another member of your organization. As the 3PL will be acting an extension of your company, it is essential that you find out if the 3PL you are viewing is the right fit for your business.
This month we’ve created an infographic to help you select the right 3rd party logistics provider!
5 Questions to Ask Before Selecting a 3PL
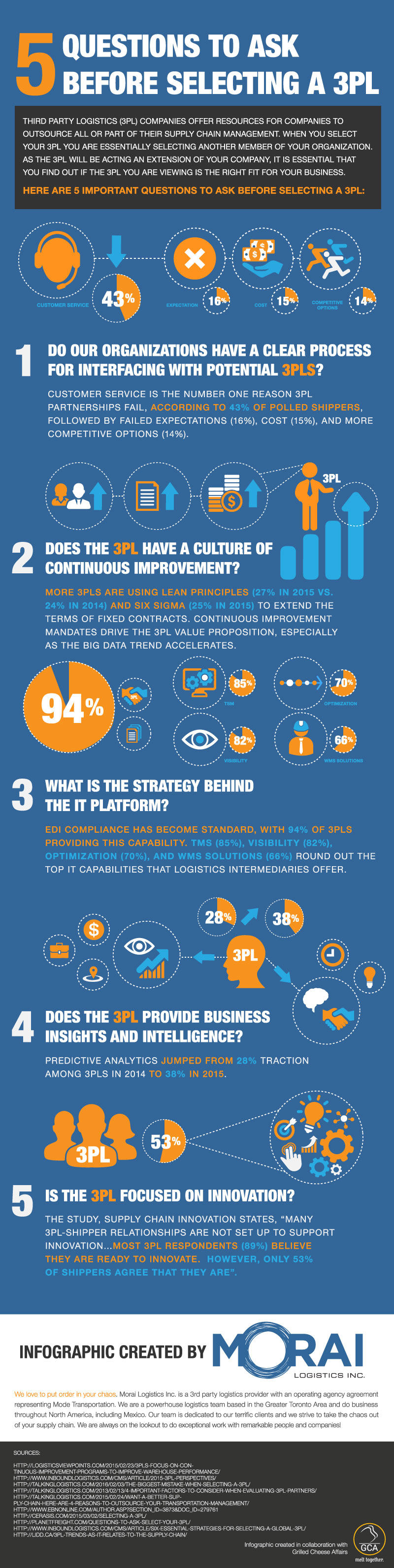
That’s it for us this week! If you liked this blog post, why not subscribe to our blog? If you’re interested in what we do as a 3rd party logistics provider, don’t hesitate to check out our services (as expressed above, we are very pro finding you the lowest total cost!). We’re also in the twittersphere, so give us a follow to get the latest logistics and supply chain news!