Ebook: The Cloud: Transforming Supply Chains Part 2
https://morailogistics.com/cloud-transforming-supply-chains-part-2/
The cloud is redefining the way in which supply chains can operate to their tremendous benefit—here’s how.
The cloud is a technology that at times goes overlooked. It doesn’t quite generate the same attention as some other tech buzzwords like blockchain or AI. Yet, the cloud is the facilitator of supply chain innovation. It is the mechanism through which digital transformation becomes a reality. Without it to pull the many disparate pieces of technology together, companies suffer from knowledge gaps due to data silos.
As such, it’s not an understatement to say that the cloud has transformed the way in which supply chains function. It has served as a kind of master key, liberating companies to have the totality of their data in one place. In turn, allowing all that data to be consolidated, interactive, and be transparently understood.
This ebook covers many of the key features that come with adopting the cloud and how those features bring numerous advantages.
In What ways is the Cloud Changing Supply Chains and What Advantages are They Gaining as a Result?
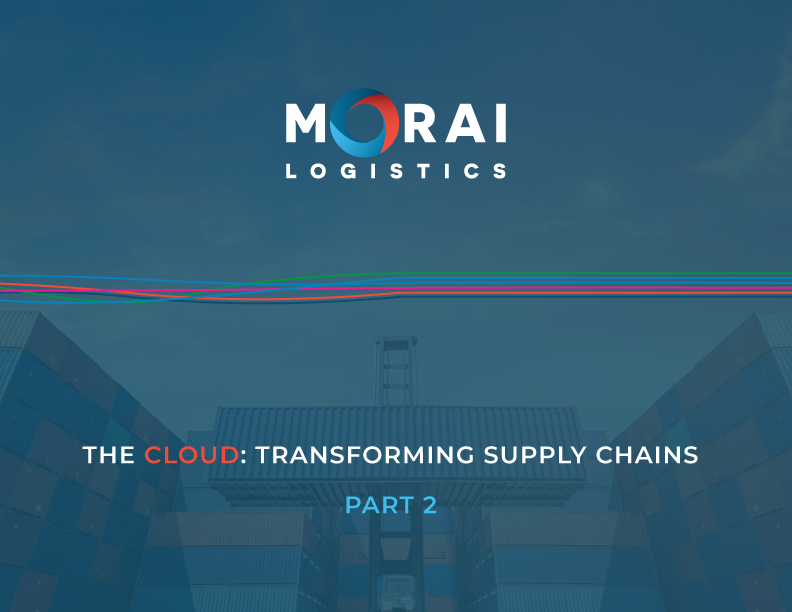
That’s it for us this week! If you liked this blog post, why not subscribe to our blog? Interested in our 3rd party logistics services? If so, don’t hesitate to check out our services . We’re also in the twittersphere, so give us a follow to get the latest logistics and supply chain news.
Supply Chain Technology 2019 – Year in Review Part 1
https://morailogistics.com/supply-chain-technology-2019-year-review-part-1/
With 2019 almost at an end, and technology having been the focus of so much of it, it’s critical to look back at some of the supply chain technology that defined it.
More than ever before the supply chain has become characterized by technology. Artificial intelligence, machine learning, automation, blockchain technology, and much more are all part of the technological advancements driving supply chains forward. 2019 saw all these innovations continue their ascent. And, while not all of these technologies have seen wide scale adoption just yet, it seems to be a matter of when rather than if.
An article by All Things Supply Chain further delves into this supply chain trend,
In the globalization era, the supply chain is more diverse than ever before. Every day new technical innovations offer the opportunity to reduce this complexity. Gartner vice president David Cearley describes this development as an “intelligent digital mesh” that “will be characterized by smart devices delivering increasingly insightful digital services everywhere”. These circumstances are transforming the supply chain from a technology-enabled procedure to a technology-centric one.
This article by Morai Logistics highlights some of the most prominent developments in supply chain technology in 2019.
Artificial Intelligence (AI)
Perhaps the most significant technology in the supply chain space, artificial intelligence had a big year in 2019. Being responsible for machine learning, several smart devices, and the driver of automation, AI is the linchpin to numerous critical innovations. What AI in 2019 showed is that it is entirely capable of taking on numerous human tasks and operations. Analyzing data, making models, predictions, and forecasting with it, route optimization, personalizing customer service are just a few things AI showed that it’s capable doing for companies over the previous year.
Analytics
If AI is the linchpin to a variety of technology, data is the life force for it. In turn, it’s through analytics that that life force can best be utilized and understood. Although analytics have been around for a while, they are growing more advanced. 2019 saw these advanced analytics grow a great deal more prominent.
A post by Gartner on the technology trends of 2019 explains,
Advanced analytics are increasingly being deployed in real time or near-real time in areas such as dynamic pricing, product quality testing and dynamic replenishment. The availability of supply chain data — such as Internet of Things (IoT) data, dynamic sales data and weather patterns — provides the ability to extrapolate the current environment to better understand future scenarios and make profitable recommendations.
Internet of Things (IoT)
The previously mentioned article by All Things Supply Chain addresses the impact IoT is set to have on supply chains,
In the future, the number of networked devices will increase enormously, thus boosting efficiency and productivity in supply chain. Gartner estimates the number of networked devices will be 25 billion in 2021. In the future supply chain, for example, these could be smart sensors on manufacturing floors in order to efficiently manage planned and predictive maintenance work. These sensors could also be used to closely monitor and track stock and the entire inventory. Not only does this save a lot of manpower, but it also allows you to optimally plan your future production.
However, while 2019 didn’t quite reach those heights for IoT, it certainly further cemented its place in the supply chain. Adoption rates of IoT technology increased a great deal. As the year brought with it a greater focus on providing an end-to-end experience, companies began utilized IoT to help deliver that experience. And, as the above article displays, IoT adoption will only increase going forward.
Automation
Lastly, automation carried on expanding its presence in supply chain operations. Supply chains involve many tedious and repetitive tasks. Automation has allowed those tasks to be handled by machines like robots and drones. However, what 2019 showed is that automation doesn’t only mean a loss of human labour. It also means better human labour and supplemented human labour. Automation allowed workers to focus on more meaningful work in supply chains.. Not only that, but it also gave workers assistance with some of the more labour intensive tasks.
2020 Predictions: Supply Chain Technology
https://morailogistics.com/2020-predictions-supply-chain-technology/
As 2020 fast approaches, it’s worthwhile looking ahead to where supply chains are set to go in the coming year, particularly with respect to the technology that bolsters them.
Companies successfully adopting the latest and greatest technology has really become central to supply chains performing well. As such, the past year has seen companies move towards digital transformation. This is because digitization is the main mechanism through which companies can integrate the technologies they need.
As a 2020 predictions report from IDC states,
Digital transformation is now the overriding priority for most manufacturers and retailers, with the adoption of digital technologies aimed to improving efficiency and effectiveness in the shorter term while providing the opportunity to either disrupt their market segment or be resilient to others that may try.
Having said that, most companies are now in some state of digital transformation. Thus, the question then becomes what technology will they look to to best optimize their supply chains? Rather than something wholly new, it’s likely that the next year will simply see supply chains embrace more of the same, just to different degrees.
This article by Morai Logistics highlights technological developments set to take place in the coming year.
Artificial Intelligence and Machine Learning Will Become Even More Prominent
With more and more data being gathered by supply chains, it’s becoming increasingly important to utilize that data precisely. This is where AI and machine learning algorithms will come into play. By having sufficient data, machine learning can distinguish the quality data from the junk. In turn, it can use that quality data for a number supply chain functions. Key among those functions being forecasting and planning. But they are just two amongst many.
A Finance Online post further explains the importance of AI and machine learning,
Artificial intelligence (AI) will also play an essential role in making supply chains more efficient. The technology can be used to automate procedures using algorithms based on data from previous processes. Automation makes supply chains more efficient by eliminating human errors. AI also can identify patterns in the supply chain, and companies can leverage this technology to predict purchasing demands and manage inventory. This takes the guesswork out of planning and procurement, eliminating the need for planners to do the same calculations over and over.
Blockchain Adoption and Belief Will Come Gradually
Blockchain technology has gained a great deal of attention in recent years. In the past year though, some of that attention has turned sour. A great deal of skepticism has arisen regarding a variety of its limitations. At the same time, the technology has finally made some strides.
TradeLens, in particular, has elevated itself into being the largest blockchain platform available for shippers. Nevertheless, it will take some time before blockchain is trusted and adopted en masse. Until then, as will be the case in 2020, the technology will experience slow and steady progress.
Robots Will Work With (Rather Than Replace) Human Workers
Robots are an emerging presence in supply chains. As a result of this, many workers in the space have grown concerned about the likelihood of robots replacing them. While some degree of displacement seems inevitable, much of the worry is overblown. 2020 will see humans working alongside robots in supply chains. And, in many ways, this will liberate human workers.
A recent Supply Chain Digital article expands on this,
Machine learning algorithms will handle boring, repetitive tasks like data hygiene and number crunching that planners with domain experience will use to make decisions. In our customer base, technology automation hasn’t replaced humans but elevated the roles of chronically overstrained planners, allowing them to focus on work that creates the most value.
5 Supply Chain Trends to Watch for in 2020
https://morailogistics.com/5-supply-chain-trends-watch-2020/
With 2019 coming to an end, it’s important to know what the new year will bring the world of supply chains—here are 5 supply chain predictions for 2020.
The year’s almost over. 2019 saw significant changes for supply chains all across the globe. Technological advancements continued coming in thick and fast. Additionally, several preexisting innovation picked up steam. Going forward, many of 2019’s develops are set to continue into 2020. On the other hand, several supply chain changes that come next year could be entirely novel. It’s impossible to know for sure, but there are certainly some indications one way or the other.
This article by Morai Logistics highlights 5 of the most prominent supply chain trends to be mindful of in 2020.
Going Green
More than ever companies will need to make their supply chains green. That means bringing down their carbon emissions and waste. Not only will this be critical for pleasing consumers but also in avoiding sanctions by governments. Furthermore, having a more sustainable supply chain means reducing inefficiencies, further reducing costs.
An Industry Week article further expounds on the value of a green supply chain,
Transportation is the second largest source of greenhouse emissions after electricity generation, Lapide noted. He said companies need to develop energy efficient transportation operations, greatly enhance their reverse logistics capabilities, move toward green product design and take a holistic view of supply chain compliance as they become aware that their image in the marketplace depends not just on their own operations but their whole supply chain.
Focus on Integration
With technology becoming an ever-increasing factor for supply chains, integration is going to continue to be crucial going forward. In fact, even more so than before. As the number of supply chain innovations grow, it’ll become even more important to consolidate them. In turn, as data continues to be an increasingly valuable commodity for smart supply chains, integration will ensure it’s all collected and stored in the same space.
Blockchain’s Gradual Increase in Significance
Blockchain technology hasn’t quite arrived with the impact some predicted. Quite clearly it’s a promising technology, but it needs time. 2020 won’t necessarily be its breakout year, but it should be another year where it makes steady gains. There will be particular focus on TradeLens. It being the most comprehensive and highly adopted blockchain platform in the field of shipping and logistics. Ultimately, the demand for visibility and transparency in supply chains is only going to grow more pronounced. As such, blockchain isn’t going anywhere.
Automation and its Consequences
Automation is only going to become more prominent with each passing year. With that said, that move towards a less human supply chain might have costs in the short term that will become apparent over the course of the year. After all, digitization which is a prerequisite for automation, is extremely expensive and takes time to adjust to.
Trade Ready’s post explains why digitization can be detrimental to companies in the short term,
While many companies are moving to an increasingly digital workflow to reduce costs, in my opinion going digital is itself a big cost as investing in technology would be. While it will be beneficial at some point, investing in infrastructure and training humans will help to increase the productivity of supply chain and eliminate the additional cost of maintenance.
Smarter Warehouse Management with IoT
The internet of things (IoT) is integral to the earlier mentioned integration. When it comes down to smart warehouse management, having devices continually connected to the internet and giving constant feedback is vital. They allow warehouse managers to know the state of their inventory and track the performance of their operations.
TradeGecko emphasizes the importance IoT is set to have in integrating and boosting the productivity in warehouses,
That being the case, supply chain technology will likely become not only more integrated with other such tools, but will also become more specialized, as well. Supply chain teams that adopt this highly-integrated and specialized technology moving forward, then, will almost certainly spur a massive growth in productivity throughout their processes.
Ebook: The Cloud: Transforming Supply Chains Part 1
https://morailogistics.com/the-cloud-transforming-supply-chains-part1/
Supply chains are changing in a variety of ways due to technological advancements—here’s why the cloud is proving to be the most significant innovation of all.
Rapid advancements are taking place in the way supply chains operate, and companies need platforms to support them. These advancements are coming in the form of a variety of technological innovations. Namely, these innovations include artificial intelligence, machine learning, big data, the internet of things, automation, smart sensors, and much more.
However, in turn, with all these new technologies and their corresponding platforms, there comes a need for all them to work together cohesively. This means all their data and processes being consolidated and being able to interact with each other. This is where the cloud comes in. It’s the technology that binds everything together.
This ebook covers just what cloud computing is, a couple of its most important features, and why those features are of such value to supply chains.
What is the Cloud, and What Makes it Such a Significant Technology for Supply Chains?
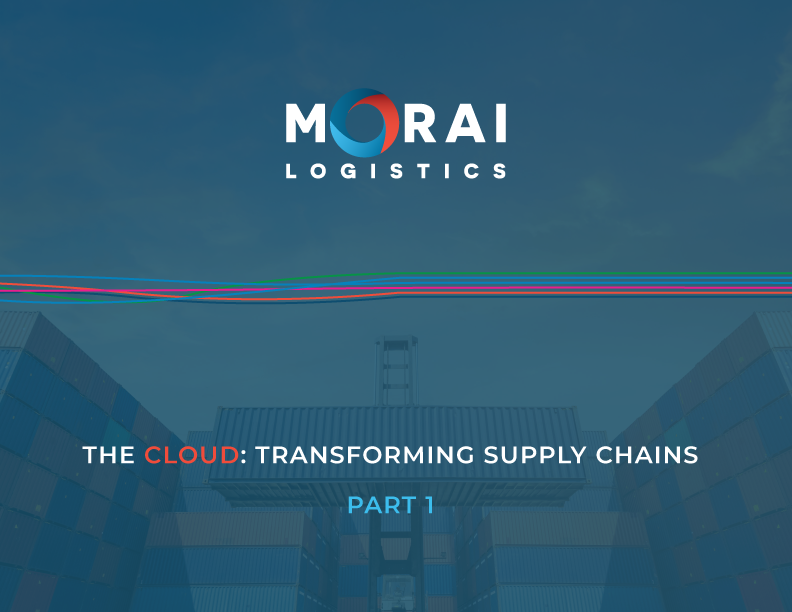
That’s it for us this week! If you liked this blog post, why not subscribe to our blog? Interested in our 3rd party logistics services? If so, don’t hesitate to check out our services . We’re also in the twittersphere, so give us a follow to get the latest logistics and supply chain news.
The 4 Greatest Hurdles Blockchain Technology Is Currently Facing
https://morailogistics.com/4-greatest-hurdles-blockchain-technology-currently-facing/
Blockchain technology continues to garner a lot of attention, but here are the 4 biggest obstacles it’s currently facing.
As supply chains continue to transform with the advent of a variety of technologies, their adoption of blockchain remains uncertain. Unlike technologies like artificial intelligence, automation, and IoT, blockchain has yet to prove itself as viable. It has displayed a great deal of promise and, in theory, could prove incredibly beneficial to a variety of industries, including supply chains. As of yet, however, there are a number of areas in which it needs to win over the masses.
CIO Dive elaborated on this earlier this year,
In its 2019 Hype Cycle for Blockchain Technologies, Gartner found most blockchain technologies remain stuck in an “experimentation mode.” The analyst firm said most applications are yet to live up to their hype, and that interest in them has waned as applications failed to deliver on their expected outcomes.
This article by Morai Logistics explains the four most significant barriers blockchain technology faces today.
Explaining it’s Value
Blockchain, in large part due to its complexity and nascency, is hard to explain. As a consequence of this, it can be incredibly difficult for decision-makers at companies to be convinced of its value. It can be reduced to a pithy line such as: blockchain is an immutable, transparent, and decentralized data base.
However, this hardly gets across the intricacies of the technology. Any elaboration on such a barebones explanation inevitably involves neologisms specific to the technology. This makes it even harder to understand than it already would be. Moreover, this is only made worse because even some that do understand the technology remain skeptical of its benefits. Thus, the burden for blockchain companies to prove the technology’s value remains incredibly high.
Lack of Maturity
In turn, just as blockchain suffers from its complexity, it also suffers from its recency. The technology has only been around for about a decade and only really taken off in the last few years. As a result of being such new technology, there are valid concerns over its maturity. Essentially, it’s yet to prove itself. It has been experimented with, yet there are very few instances of it being successful on a broad scale.
The previously CIO Dive article touched on this as well,
The immaturity of blockchain technology has been delaying its application in enterprise settings, as the majority of applications have either stalled at the experimentation space or will be in need of replacement in the near future.
Concerns About Reliability
Additionally, as blockchain technology isn’t proven, it’s hard to assuage fears about its reliability on some fronts. For example, how will it scale? So far, it’s proven not to be able to handle a large number of transactions, marking a considerable liability for large companies. Not only that, but there are additional concerns about how slow its transactions are due to the verification required of them.
Difficulty of Collaboration
Finally, in order for blockchain technology to work, it requires all actors involved to be on board. In the case of a supply chain, this means getting all the disparate parties involved to buy into the technology. Furthermore, this issue gets only more complicated as all parties also have to agree upon the best platform and development project for the technology. Without one outright blockchain leader in the field, this can be incredibly testing.
A recent Supply Chain Dive post explains the best way forward for blockchain collaboration,
Instead of having competing blockchain projects under development at different companies, success stories include the formation of standalone companies or consortiums in order to better articulate a strategy around a specific technology.
What Does End-to-End Supply Chain Transparency Look Like?
https://morailogistics.com/end-end-supply-chain-transparency-look-like/
As consumer demands for transparency grows, the need for end-to-end supply chain visibility grows along with them—so what does such a supply chain look like?
Many of the changes in the way supply chains operate in recent years have come due to the pressure placed upon them to be more transparent. Customers (and others) want to know everything going on in a supply chain. They want to know what goes into creating their products, where they come from, how they are maintained, and much more.
Harvard Business Review underscored the importance of supply chain transparency in a post earlier this year,
Companies are under pressure from governments, consumers, NGOs, and other stakeholders to divulge more information about their supply chains, and the reputational cost of failing to meet these demands can be high.
As a result of this pressure, organizations are having to ensure that know about every aspect of their supply chains. That means them knowing their supply chain operations from start to finish. From where their raw materials are coming from to their product’s journey right into the customer’s hands. Moreover, they have to be able to easily share this information with their customers throughout the process. This is where end-to-end supply chains become a necessity.
This article by Morai Logistics explains what an end-to-end supply chain is and the prominent components such a supply chain needs for transparency.
What is End-to-End?
Investopedia defines end-to-end as,
End-to-end describes a process that takes a system or service from beginning to end and delivers a complete functional solution, usually without needing to obtain anything from a third party.
In the context of supply chains that means taking care of all the disparate operations that make them up. By having control of the totality of a supply chain, companies are able to guarantee that they know everything that’s going into them. In turn, reassuring their customers that their products are above board, ethical, and of good quality. But for their customers to be entirely satisfied, companies need to provide the necessary transparency throughout their operations. As such, their supply chains require certain characteristics to make that possible.
Digitized
The foundation upon which end-to-end supply chain management is built upon is digital transformation. The reason for this is that it enables the many technological tools that are needed for it. This includes automation, AI, machine learning, IoT, cloud computing, and more. Furthermore, it’s through such technologies that increased transparency becomes a reality.
For example, automation can increase the accuracy of data collection, making it easier to follow daily operations. Another is smart sensors, that can be put on the packages being shipped, providing information about where they are and what conditions they’re experiencing. Thus, it is through digitization that supply chains become intelligent and data driven. Consequently, they have more information for companies to provide their customers.
Connected
End-to-end supply chain should mean end-to-end visibility. A recent Supply Chain Digital article emphasizes this
A truly connected end-to-end supply chain has the aim to reach 100% visibility in real time which creates an integrated view across the enterprise, including, suppliers, retailers, manufacturers, outsource partners, and customers. This then allows companies to easily see any inbound problems and fire up tailored solutions where needed.
However, in order in ensure that there are no gaps in this visibility, supply chains require greater integration. Particularly, they need to have all their processes integrated. While some of that is achieved by social collaboration and dynamic strategy, that in of itself isn’t enough. Digital connectivity is equally important, as a well as having a central platform for all data to be aggregated. Hence the need for digital transformation.
Traceable
One final component of transparency that may gain traction going forward is traceability. With the growth of blockchain, many are starting to place importance on being able to follow each transaction in a supply chain.
An ASQ article from earlier this year points out,
Traceability is also gaining prominence as a key issue, and permissioned blockchains provide one way to make this happen with sensor data and transaction data.
Digital Transformation: Top 5 Supply Chain Benefits
https://morailogistics.com/digital-transformation-top-5-supply-chain-benefits/
Digital transformation has become a big buzzword lately, but it is nonetheless key to companies having well functioning supply chains going forward.
There has been an almost overnight paradigm shift regarding attitudes towards digital transformation. It has gone from being a goal to achieve at some nebulous future date to something that is a matter of survival. Companies of all kinds have come to see the numerous potential benefits of digitizing their practices and are embracing it as a result. The same is true of supply chains. Perhaps even more so.
An article by McKinsey explains as much,
McKinsey research suggests that, on average, companies that aggressively digitize their supply chains can expect to boost annual growth of earnings before interest and taxes by 3.2 percent—the largest increase from digitizing any business area—and annual revenue growth by 2.3 percent.
This article by Morai Logistics covers the top 5 advantages supply chains that digitize their operations are set to experience.
Decision-Making
A critical component of a healthy supply chain is the framework in place that drives its decision-making. Through the technological advancement digital transformation brings with it, that framework evolves as well. Getting access to machine learning in particular means supply chain managers can have very accurate predictions at their disposal. Which in turn can help them be much more precise with their decision-making.
As the earlier mentioned McKinsey article outlines,
Machine-learning systems can provide supply-chain managers with recommendations for how to deal with particular situations, such as changing material planning and scheduling in response to new customer orders.
Automation
In turn, digital transformation also unlocks automation. Which is set to play an enormous role in boosting supply chain productivity and efficiency. It does this in several ways. This includes reducing manual errors, completing laborious tasks faster, and making data collection more reliable and accurate. Automation is central in making tedious, repetitive supply chain work faster and more accurate, while involving less waste.
Customer Experience
Moreover, digitization brings with it a significant improvement to the customer experience companies can give their clients. This is because it enables clients to have end-to-end engagement. They can track their orders throughout the shipment and delivery process. This gives customers the transparency that they’re after and the peace of mind that comes with it.
Integrated Processes
Additionally, supply chains have gotten larger and more complex over the years. This is in large part due to the opportunities and costs globalization has brought with it. As such, it’s more important than ever for the many parts that make up a supply chain not to be silo’d but rather be integrated into one system where they can all be followed. Digital transformation means being able to have a single data management platform where all the disparate parts of a supply chain can be kept track of. This also means less resources and time spent on keeping up that tracking.
Future Growth
Finally, it’s important to keep in mind that digitization isn’t just some checkmark or objective to reach and move on from. It’s a mindset, culture, and infrastructure that allows for continued innovation and access to future technological advancements. It’s a foundation from which all future development can be built upon.
Slack addressed this in a post last year,
New technologies will continue to shake up customer expectations and processes. A digital business builds resilience by replacing rigid structures and inflexible processes with a workplace culture and infrastructure that can respond and adapt to new demands.
The 7 Greatest Obstacles Supply Chains Face Today
https://morailogistics.com/the-7-greatest-obstacles-supply-chains-face-today/
As supply chains continue to get larger, they also continue to get more complex and complicated, leading to a number of challenges that they have to overcome.
Today’s supply chains are facing a whole host of new demands and hurdles. Supply chains are larger than ever. Not only that, they’re more sophisticated than ever before as well. While both of these things have a number of upsides, numerous obstacles arise as a result of them. Growth and progress come with difficulty, after all.
Blume Global highlights some of the ways modern supply chains have to evolve to the new demands placed upon them,
The modern supply chain must evolve to meet new demands and supply chain challenges, and supply chain managers need to plan ahead to keep everything flowing smoothly. A combination of consumer expectations, more routes to market, international complexities and other factors creates significant challenges throughout the supply chain network.
This article by Morai Logistics covers the 7 biggest challenges supply chains are currently facing.
Technology
With the rapid advancements in technology pertaining to supply chains, not integrating them is a considerable liability. Whether it be artificial intelligence, machine learning, automation, or some other innovation, they are all critical to running an optimal supply chain. More broadly speaking, that’s why digital transformation is such a fundamental part of the modern day supply chain.
Cybersecurity
With that being said, taking your supply chain digital also brings about further risk. It opens up your operations to the threat of hacking and other cybersecurity vulnerabilities. These can slow down down, disrupt, or halt the running of a supply chain. Thus, it’s of the utmost importance that, when digitizing, companies also secure their new technologies. This includes vetting their partners and vendors.
Forecasting
Given the previously mentioned increased size and complexity of the modern day supply chain, forecasting is more important than ever. As such, companies have to be as precise as possible with their supplies to meet customer demands.
The Houston Chronicle explains,
Proper forecasting helps ensure you have enough supply on hand to satisfy demand. An overestimation of demand leads to bloated inventory and high costs. Underestimating demand means many valued customers won’t get the products they want.
Overseeing Inventory
Tying into forecasting, is the need for the management of inventory. In order to have the adequate amount of supplies on hand to satisfy demand, companies need to be able to closely track their inventory. With that being the case, having proper count, visibility, and quality assurance of inventory is critical in today’s market. In order to meet these requirements, companies need to invest in the proper inventory management software and technology.
Market Expansion
Companies looking to grow will have a harder time than ever in today’s market. A company that expands its supply chain to new regions has to contend with a variety of issues. This includes new policies, cultural impediments, governmental incentives and disincentives, political instability, weather, and more. Without covering all these bases, a company is destined for failure.
Customer Service
Due to the all technological advancements mentioned earlier, customers are more particular in their demands than ever before. They want their orders delivered faster, with greater care, and for less. And it’s up to companies to cater their supply chains to those demands. In turn, however, through the utilization of technology such demands are more feasible than ever too.
Globalization
Finally, in many ways, globalization’s central to many of the obstacles outlined here. The market’s gotten larger, more interconnected, and complex. With that comes uncertainty, confusion, and externalities that are hard to prepare or mitigate for. Thus, companies have to account for these factors when constructing their supply chain strategies.
Ebook: Robots, Cobots, and Bionic Workers – the Future of Supply Chains
https://morailogistics.com/morai-logistics-ebook-robots-cobots-bionic-workers-future-supply-chains/
The nature of supply chains are quickly changing with advent of robots, but that doesn’t mean human workers don’t have a place in them—here’s what the future of supply chains could look like.
Much has been made of the advent of autonomous robots and what they mean for the future of supply chains. Questions have been raised over their growing prominence and whether human workers are set to be replaced. Recently, however, with cobots and bionic workers coming into the picture a new wrinkle has been added to this new paradigm.
It appears that robots and humans are no longer in a zero-sum game but rather can be most productive together. We’ve already talked about cobots, just what they are, how they bridge the human-robot divide, and how they will help supply chains. But they are just one component of an evolving work environment in supply chains.
This ebook explains what autonomous robots, cobots, and bionic workers are, why each of them are successful, and why supply chains will be using all three going forward.
What Does Work in Supply Chains Look like in the Future?
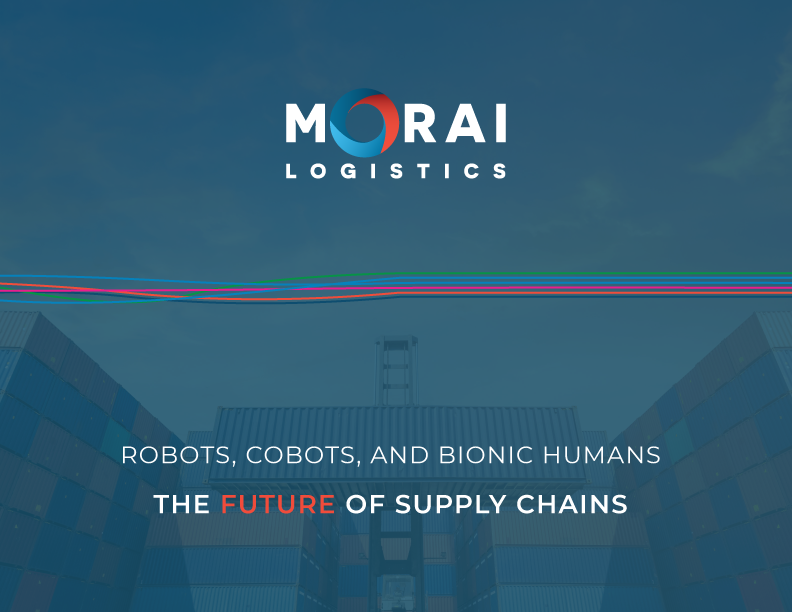
That’s it for us this week! If you liked this blog post, why not subscribe to our blog? Interested in our 3rd party logistics services? If so, don’t hesitate to check out our services . We’re also in the twittersphere, so give us a follow to get the latest logistics and supply chain news.